Engineering
Airex Rubber Products can assist you with creative, cost effective designs, tooling, and aid in their implementations.
Product Design and Engineering
Look for Airex Rubber Products to solve your product design and engineering requirements.
As a leader in custom design and engineered rubber products, Airex product engineers can assist you in evaluating your product requirements, creating cost-effective designs, and identifying materials suitable for required applications. Dedications to Quality, Customer Satisfaction, and usage of state-of-the-art technologies are our first priorities, resulting in the development of products to exacting standards.
Our diverse customer base of aerospace, medical, automotive, petroleum, and military application has provided a broad degree of product knowledge and design standard compatibility. Complete design and manufacture packages are a direct result of this knowledge and the ability to access the expertise of an entirely in-house team of professionals.
- Example: A process engineer requires a high-performance elastomer and related fixturing to perform in various surface treatment applications.
Airex engineers design, prototype and provide the technical assistance for successful implementation.
Airex can provide a cost estimate for Design and Manufacture to your requirements. A budgetary quote can be provided to establish development cost and conceptual design. Please call to discuss specific requirements and to determine the associated required reference material.
- Example of a typical budgetary Design and Make Proposal: After receipt of customer-supplied reference material regarding product drawings, specifications, or associated products, the design and engineering staff will evaluate, design, and provide a budgetary proposal using current drafting methods on our latest CAD Systems.
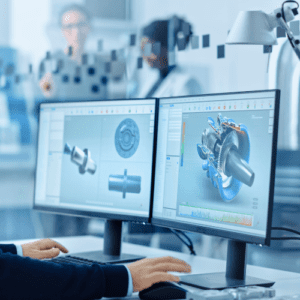
Development
Custom rubber compound products developed to satisfy specific customer requirements and maintain the integrity of existing compounds.
Material Development Laboratory
The Airex Rubber Products Research and Development Laboratory performs chemical and physical testing to ensure that all products meet or exceed our customer’s specifications. Airex currently offers a broad spectrum of compounded elastomers designed for maximum performance and maintains a formulary of hundreds of proprietary compounds, each specifically designed to meet the needs of our customers and the markets they serve. In cases where no specification exists or unique material requirements need to be met, we have the expertise to custom formulate new compounds to meet these situations.
Most applications can be satisfied from our extensive existing material compounds. Custom rubber compounds can be developed to satisfy your specific requirements. Please inquire about your specific applications.
The laboratory is under the direct control of our Chemist.
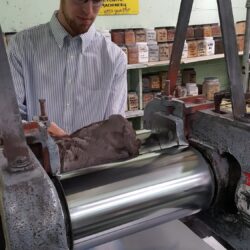
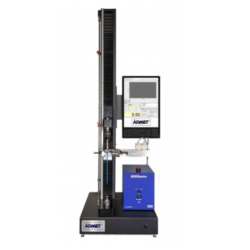
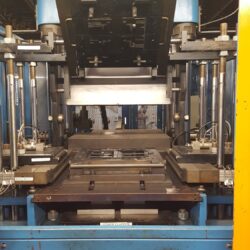
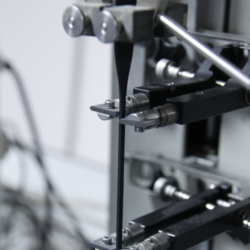
Tooling
Complete in-house control over construction of elastomer mold tooling and fixtures used in conjunction with rubber masking products.
Machine Tool Division
Elastomer mold tooling manufactured using CNC, 3D printing, Manual and Waterjet technologies.
The Airex Tooling Division is capable of handling a large range of machining requirements, including molded parts up to approximately 40″ in diameter and fixtures up to 48″ in diameter.
Our mold makers/toolmakers are proficient with the design and manufacturing of single and multi-cavity molds. They are experienced in prototype, short and long-run production, and the manufacturing and use of jigs, fixtures, gages and dies.
Our toolmakers are adept in working with various materials, i.e. plastics, aluminum, aluminum alloys, brass, bronze, steel, steel alloys, tool steels, and stainless.
Our expertise enables us, as required, to design our molds to accept a customer’s metallic part in either a semifinished cast state or a fully machined state, allowing a superior rubber-to-metal hot bonded assembly.
A full complement of turning, milling, and general machining equipment, both C.N.C. and manual are housed in our on-site tooling division. This state-of-the-art equipment, combined with the expertise of our mold makers and product design engineers, enables us to meet customer requirements. We continually strive to expand our capabilities to meet existing, as well as new customer needs.
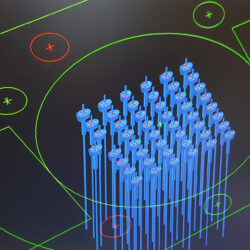
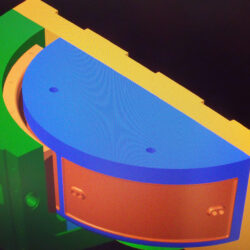
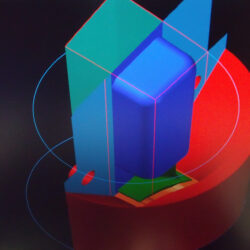
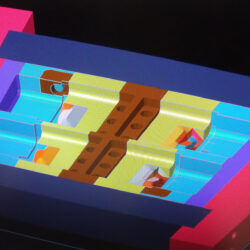
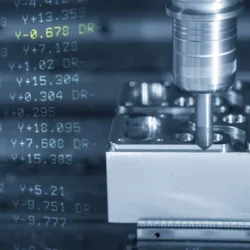
Production
Our Production Division is capable of molding rubber products using a wide range of steam and electric, as well as extrusion and die cutting presses.
Production Division
Our Production Division is capable of molding rubber products using a wide range of steam and electric presses as well as extrusion and die cutting presses.
Elastomers used in the production of specific parts are milled in-house to the specifications and formulas determined by our Chemist. The molders work to exact specifications dictated by our customer requirements as well as mold size and material characteristics. At Airex, we manufacture using a quality management system based on AS9100 and ISO9001.
The following is a list, by no means comprehensive, of precision molded masking materials commonly used for surface treatment operations. Click here for a more detailed Materials list.
Preban 3, 5, and A-9666 are premium materials designed for the high temperature and abrasion resistance of thermal sprayed coatings.
- Preban M was developed to meet the strict requirement for processing of orthopedic implants through thermal spray coating operations.
- A-9560 is designed for extruded materials used for high temperature and abrasion resistance.
- A-6040 provides excellent resistance to vibratory finishing and wet media abrasion operations.
- A-7703 was developed for maximum dry abrasion resistance of shot, glass or grit blast operations.
- A-3688 or A-2620 and A-8770 are just a few of our chemical and acid-resistant materials used for plating and commercial solvent applications.
- A-1550 material is excellent for airflow/Waterflow fixture masking. Core plugs, edge protectors, and any application where elongation and compression resistance
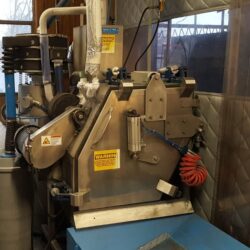
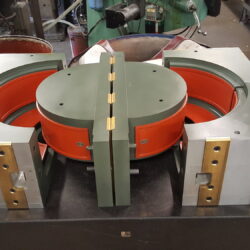
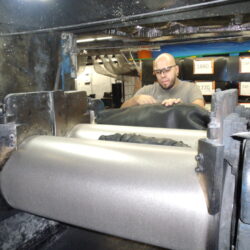
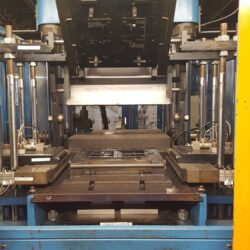
Rubber Masking
Servicing Jet Engine Manufacturers and Overhaul services with masking products developed for surface treatment operations. Materials developed for Metallurgical and Chemical processing. Complete tooling packages designed and manufactured to exacting tolerances.
Note: Our material isn’t a mix of parts A and B. It’s created from a real rubber base, mixed in a rubber mill, and each batch is 100% tested to meet customer needs. It’s made to last and ensures quality for your application, serving as a reliable hard rubber mask.
Surface treatment process with reusable rubber masking products:
Airex serves jet engine manufacturers and overhaul services, offering specialized masking products tailored for surface treatment operations. Our materials are developed for metallurgical and chemical processing, and we provide complete tooling packages designed and manufactured to exacting tolerances. Our high-precision reusable rubber masking products are specifically crafted for diverse industries, such as jet engine manufacturing, overhaul services, aerospace/defense, medical implants, commercial, and more.
Precision Masking Design with Siemens NX or Customer Provided Part
Utilizing Siemens NX design software, Airex engineers accurately design each mask to your exact specifications, ensuring a perfect fit with your customer provided parts or models. This results in exceptional precision and adherence to even the tightest tolerances.
Rapid Application and Residue-Free Removal
Airex masks seamlessly snap onto parts in mere seconds, eliminating the time-consuming and labor-intensive process of manual masking tape application. Moreover, they can be removed effortlessly without leaving any residue, further refining the surface treatment workflow.
Enhanced Productivity and Reduced Rework
Traditional Tape masking methods often lead to inconsistencies and rework, especially for critical and complex parts. Airex masks address these challenges head-on, dramatically reducing rework and scrap rates. This, in turn, enhances productivity and overall cost savings and improves lead time for your customers. Plus, with our masks, anyone can use them – no need to rely on just one person.
Reusable, Repeatable, and Versatile
Airex has developed a range of specialized compounds for different processes. Through partnerships with major customers in the Defense/Aerospace industries. Airex masks are engineered for long-lasting performance, offering reusability over and over again. Their repeatable design ensures consistent results, regardless of the operator, making them a valuable asset for any surface treatment operation.
Common application are as follows:
- Plasma & Thermal Spray Masking
- Cold Spray Masking
- Shot Peening Masking
- Grit Blasting Masking
- HVOF Masking
- Electron-beam physical vapor deposition (Pre and Post) Masking
- Cat-Arc (Pre and Post) Masking
- Plating Masking
- Vibratory Bowl Finishing Masking
- Chemical Processing Masking
- Polyamide Masking
- Plasma Tapes
- Paint and Powder Coating Masking
- FOD elimination Masking
- Part Protection Masking
- Any Custom Masking
Many more custom masking for aerospace components, such as:
- Turbine blades
- Compressor Blades
- Vane (Nozzle) Masking
- Combustors
- Turbine Rotor and Stators
- Medical Implants
- Ducts and Housings
- Racks
- Disks
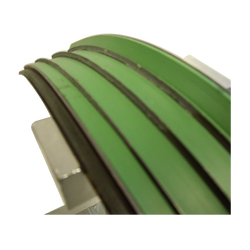
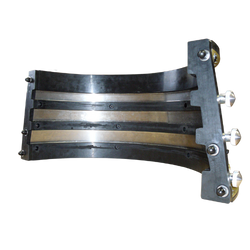
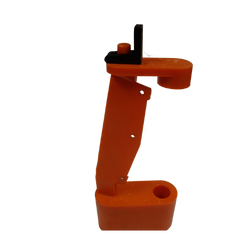

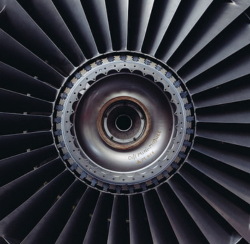
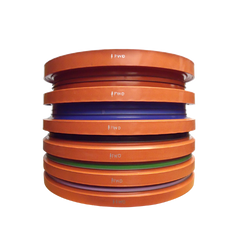
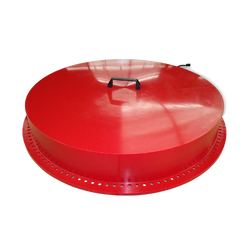
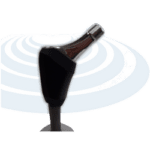
3D Printing & Fabrication
High-Quality 3D Printing – From Prototype to Production
Need high-quality 3D-printed parts? Airex makes it easy. Whether you’re developing prototypes, custom components, or full production runs, we provide precision, reliability, and efficiency every step of the way.
Our 3D Printing Capabilities
We specialize in manufacturing high-performance parts and fixturing for turbine blades, engine components, aerospace industries, FOD, and many other industrial applications—all at competitive prices. Airex now offers metal 3D printing capabilities, using Inconel and stainless steel to produce durable prototypes and custom parts.
Our advanced 3D printing technologies include:
- Metal 3D Printing: Utilizing Inconel, stainless steel, and other materials for high-strength prototypes and custom solutions.
- Fused Deposition Modeling (FDM): Fast and cost-effective for durable prototypes.
- Selective Laser Sintering (SLS): Strong, functional parts with excellent detail.
- Stereolithography (SLA): High-resolution prints for intricate designs.
- Additional processes tailored to your specific needs.
From concept to completion, Airex delivers quality, precision, and innovation to bring your ideas to life. Get in touch today to discuss your project!
GET STARTED
To request a quote, email us at [email protected] with details about your application and requirements. If you need design modifications, let us know!
Please provide:
- CAD model (STP, Parasolid, NX, or SolidWorks file)
- Material type
- Quantity needed
- Preferred printing process
- Any special instruction(s)
Once we receive your information, we’ll get a quote to you as soon as possible.
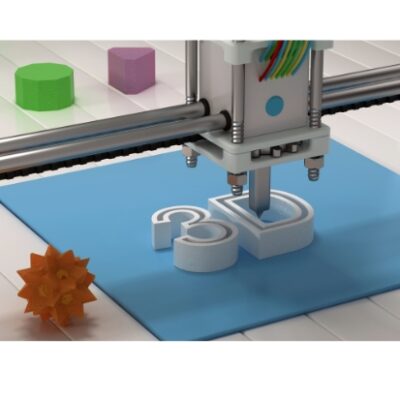
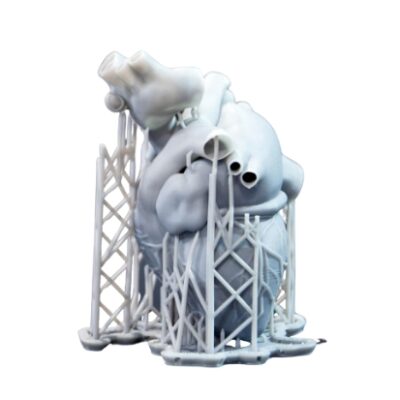
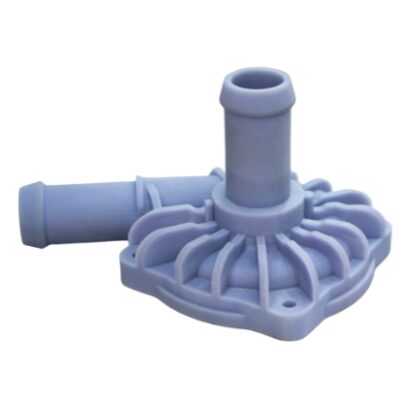